AGCbox is the only off-the-shelf solution designed for machine and tractor manufacturers who aim to fully automate their off-road vehicles. This positioning and guiding device includes a Safencing function enabling machines to operate legally in Europe without requiring human supervision.
What is the most striking detail of your solution? GNSS RTK/Safencing
This is the first GNSS-RTK solution that guarantees the machine will remain in its working area. Agreenculture does not make retrofit kits for private individuals, but rather is designed to be integrated alongside the design of the machine. The aim is to integrate the necessary safety components to ensure that the machine operates completely autonomously without local human supervision or in close collaboration with the tractor manufacturer.
How does the tractor with your autonomous kit navigate and plan its work and paths?
Machines automated with our AGCbox system are guided by our real-time secure positioning and guidance system, using our own RTK-GNSS technology, with centimetre-level accuracy. The first step is to carry out a survey, which maps out the first row, obstacles and the certified safety contour (which ensures that the machine and its implement do not leave the working area).
The user can then generate his mission by choosing on the AGC-cloud the machine used and the tool attached or towed. The mission is then simulated and validated before being sent to the machine’s AGCbox. A radio remote control allows the machine to be moved in manual mode and to switch to autonomous mode in complete safety. The machine can then be launched with the mission management application.
The machine then follows the mission orders from one row to the next. It can calculate its own U-turns according to the space it has to turn, its tool and the Safencing constraints. The turns and the navigation between rows are adjusted real-time by the machine itself.
How are implements operated and controlled by your system?
We work directly with machine manufacturers, which gives us full control over the implementation and management of the machine and its tool. We can control the tool by communicating through a dedicated technological brick. We adapt our approach to the customer’s specific requirements, to ensure optimum system performance. We are also able to offer a remote machine control service. So you can take control of your machine quickly and safely.
What safety features do you offer?
To ensure that the machine does not leave its working area, we have developed a plug &play safety component called Safencing. This is a virtual safety barrier certified by an external certification body, that allows the full machine to be certified and ensures that the machine remains within its working area. This is available for most tractors on the market.
We also have off-the-shelf safety computers (ECU’s) that can be integrated into the machine to manage the entire implement, as well as the machine, sensors, bumpers, LiDAR, emergency stop buttons, buzzer, etc. to enable obstacle detection and to stop the machine in a safety relevant situation. If the machine stops, the owner or operator is alerted with the error code, the emergency stop is triggered, front bumper activated, etc.
It is also possible to add cameras that allow visual monitoring of the implement’s work and its direct surroundings. Or to carry out a check to understand why a machine has stopped.
What kind of (farm) work can your system do autonomously?
Our system can make any off-road machine autonomous. We’ve worked on a range of tools, from soil preparation and seeding to mechanical weeding, fertilisation and localised spraying.
Can you switch off autonomous mode and continue as a manned tractor for difficult work/circumstances and road transport?
In fact, it is possible to use manual mode to go out on the road with one person inside the cab. The autonomous mode can be remotely deactivated.
We are currently working on the possibility of controlling robots remotely using teleoperation. This feature will allow you to manipulate your robot remotely to unblock it when it finds itself in a complex situation, while keeping our safety system active to ensure maximum safety during manipulation. This is made possible by the presence of several cameras covering all angles of the robot, ensuring an overview and optimum handling conditions.
How many units do you currently have in the field and where?
We currently have 100 AGCbox in use worldwide.
We have equipped various machine manufacturers, such as Karl from Kuhn, RX-20 from Pellenc, Kfast from Fede and M7 from Kubota, with stand-alone solutions. And we have also worked with other manufacturers.
What is the (estimated) cost price per ha compared to the costs of a manned tractor?
For mechanical weed control in open fields, with a farm of 160 hectares, farmers identified a cost saving of €19,500 per year. Of course, this will depend on the machines, the farms, the types of crops and the work required.

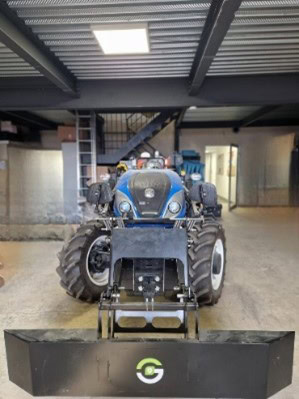
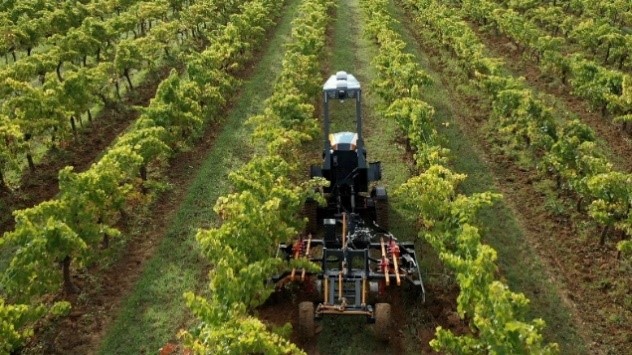
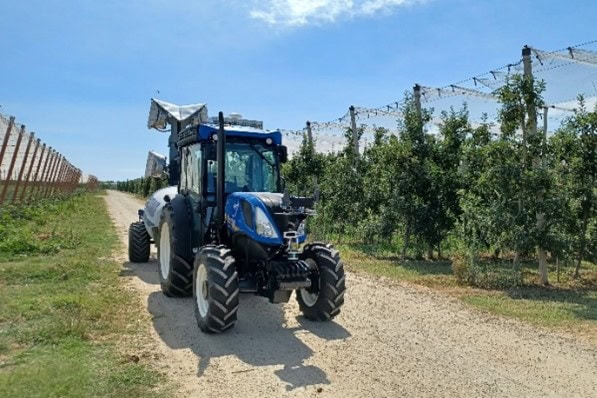
Company name and nationality | Agreenculture (France) |
Company or product website | Agreenculture – www.agreenculture.fr |
Product name | Autonomy kit equipped with AGCbox |
Suitable brands and tractor/vehicle models | Off-road machines |
Technical requirements for tractor/vehicle | Automatic gearbox and features to be used for implements to be driven by wires |
Is the solution Isobus compatible? (yes or no) | YES, compatible and ready to be certified |
Possible minimum and maximum driving speeds in autonomous mode | 2 km/h (1.24 mph) 10 km/h (6.21 mph) |
Main components autonomous retrofit kit | 3 AGCbox types: – ENS : embedded navigation system – ESA : embedded smart antenna – ARP : surveying system – CAUIS : machine safety ECU – CLEOS : implement safety ECU – CLOVIS : perception ECU |
Operator or driver nearby required (yes or no) | No |
Price (in €/US$) | HW + SW + manufacturer integration costs + certification = €30,000 to €60,000 |
Countries the product is for sale/rent in 2024 | Europe, Asia and South America |